Design automation in use: Assembly fixtures
What is an assembly fixture?
Assembly fixtures are essential tools used in manufacturing to secure and align components during assembly, ensuring accuracy and consistency for high-quality products.
A 3D printed assembly fixture with an integrated toggle clamp to keep industrial parts firmly in place during assembly operations
What are the benefits of assembly fixtures?
Precision and consistency. Assembly fixtures ensure that components are positioned accurately and consistently. This helps maintain product quality and reduces defects caused by human errors in manual assembly.
Efficiency. By holding components in the correct position, assembly fixtures speed up the entire process. Workers can quickly fit parts together without the need to measure or adjust their positions repeatedly.
Safety. Some assemblies involve delicate or hazardous components. Fixtures can hold and secure these parts safely, reducing the risk of damage or injury during the assembly process.
Automation. In automated assembly lines, fixtures are critical for enabling robots and machinery to pick up and place parts accurately, leading to increased productivity and reduced cycle times.
Complex assemblies. For assemblies with multiple components that need to fit precisely together, fixtures simplify the process by guiding the assembler through the correct order and alignment.
Repeatability. Fixtures ensure that the same assembly process can be repeated consistently, which is crucial for mass production and maintaining product quality over time.
Quality control. During assembly, fixtures can incorporate measuring devices or sensors to verify the correct alignment of parts, ensuring that products meet the required specifications.
Ergonomics. Assembly fixtures can be designed to improve worker ergonomics, reducing strain and fatigue during repetitive assembly tasks.
Cost savings. While the initial investment in designing and building an assembly fixture may be significant, it can lead to long-term cost savings by reducing errors, rework, and production delays.
Streamlining the fixture design process
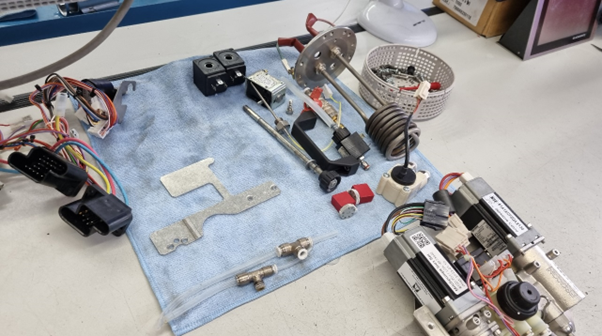
Image copyright: DB
DB have successfully embedded design automation into this process to great effect. Using fixturemate software has made the fixture design process simple and user-friendly, and has reduced demand on the core design team.
Engineering teams can be unburdened by design bottlenecks
fixturemate simplifies intricate CAD operations, making them intuitive and user-friendly. You can quickly master key design functions without the need for advanced CAD software knowledge or AM-compliant design expertise. With fixturemate, you can effortlessly generate support structures for your parts and employ advanced features like nested geometries and boolean operations to create fixtures that perfectly fit custom-shaped components.
By automating parts of the fixture design process, fixturemate saves valuable time and costs, allowing your design team to focus on high-priority tasks. The web-based software streamlines the creation of custom fixtures without requiring extensive CAD expertise. With fixturemate, you can import your parts, adjust a few parameters, and have a bespoke fixture designed and produced that same day.
A secondary design team can configure a design based on set parameters
Feedback loops between operators and designers, which were once complex and time-consuming, are now streamlined because the maintenance team is given a level of autonomy: they now have the ability to create bespoke fixtures and optimize their production tooling independently. This shift in responsibility frees DB's core design team from the burden of manual fixture design, and any design revisions that might come with that. They are free to focus their efforts on the priorities.
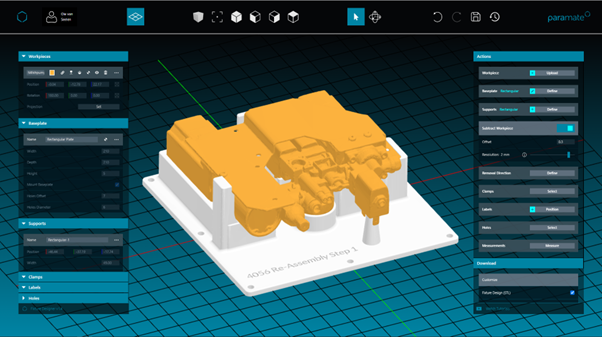
Image copyright: DB
Integrating 3D printing as a manufacturing process accelerates operations further
In terms of cost, an FDM 3D printer is getting cheaper and more capable every day. They can be quickly and easily commissioned and can produce sharp, detailed features, or smooth, organic contours. A range of 3D printing technologies are available, which cater to a range of use cases.
You can 3D print materials with useful properties for a workfloor, such as toughness, chemical resistance, and temperature resistance. Different materials can be combined for a range of design properties.
Features like embossed text labels are easy to create in fixturemate, and are easily legible on the resulting 3D printed part, so workfloor operators can quickly and clearly understand how to use it when it’s deployed in production.
Tooling can be manufactured locally
Fixture designs can be 3D printed locally, at a fraction of the operational costs of more traditional manufacturing techniques. Design automation reduces the need for external coordination and allows for more last-minute adjustments. Fixtures can be designed iteratively to road-test different design features in the same day. Multiple tools can be produced, with repeatable dimensional accuracy, for as many operators as needed. Should any fixture fail, it’s quick and easy to replace in just a few hours.
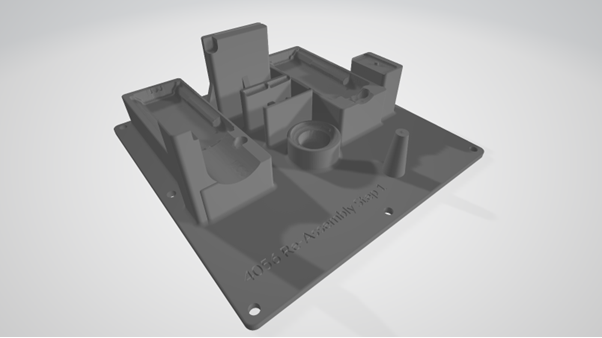
Image copyright: DB
The powerful combination of design automation and in-house 3D printing enables Deutsche Bahn to scale their internal design processes, creating a wide range of fixtures for various assembly processes within their own facilities. The implementation of an automated design workflow has resulted in increased efficiency, process flexibility, and significant cost savings for the organization.
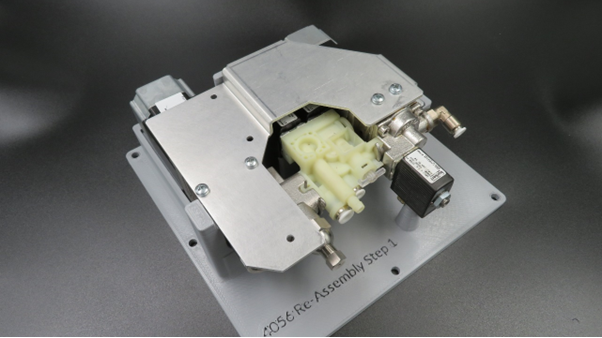
Image copyright: DB
How could design automation help you?
Assembly fixtures remain a vital part of the manufacturing process. They streamline operations, improve product quality, and enhance overall manufacturing efficiency. They are tailored to the specific needs of each assembly task, providing a custom solution for holding, positioning, and guiding components during production.
You can automate the design of these parts quickly and easily using fixturemate, our web-based design automation software. All you need to do is upload your workpiece and configure standard design features, and the software will automate the rest. CAD expertise is optional!