Design automation in use: Bonding and welding fixtures
What are bonding and welding fixtures?
In manufacturing and construction, joining materials together through bonding or welding is a common practice. Bonding fixtures and welding fixtures are specialized tools used to securely hold and position the materials during the bonding or welding process. They act as reliable guides, ensuring precise alignment and placement of the materials, and facilitating strong and consistent bonds or welds.
These fixtures find applications in diverse fields, from automotive assembly to aerospace manufacturing, where reliable bonding or welding is crucial for creating durable and high-quality products.
The benefits of bonding and welding fixtures
Bonding and welding fixtures offer several significant advantages in the manufacturing and construction processes.
Enhanced precision. By securely holding and aligning materials, bonding and welding fixtures ensure consistent and precise bonding or welding operations. This results in strong and reliable bonds or welds, reducing the risk of defects or failures.
Improved efficiency. Fixtures streamline the bonding and welding processes by allowing easy positioning and rapid loading and unloading of materials. This increases the overall efficiency of the assembly or manufacturing operations.
Cost savings. With enhanced precision and efficiency, bonding and welding fixtures help reduce material waste and decrease the need for manual adjustments, ultimately lowering production costs.
Ensured safety. Fixtures provide a stable platform for materials during bonding or welding, reducing the risk of accidents and ensuring the safety of workers.
Consistency and quality. The use of fixtures ensures uniformity in bonding or welding results across multiple products, maintaining a high level of quality control throughout production.
Adaptability. Fixtures can be designed to accommodate various material sizes and configurations, making them suitable for a wide range of bonding or welding tasks.
Complex operations. For intricate or irregularly shaped materials, bonding and welding fixtures offer stability and precision, enabling accurate bonding or welding in challenging scenarios.
Flexibility in automation. Bonding and welding fixtures are compatible with automated manufacturing systems, enabling seamless integration into computer-controlled production lines.
Shorter setup times. With repeatable setups, switching between different materials becomes quicker and more efficient, reducing downtime and increasing overall productivity.
3D printing bonding and welding fixtures
Traditionally, bonding and welding fixtures need some initial investment in design and fabrication, but they offer long-term benefits which make them cost-effective over time.
By pairing design automation with 3D printing, this initial design and fabrication investment can be short-circuited, so they can be produced at a fraction of the time and costs.
Using fixturemate, anyone can design and configure bonding and welding fixtures – even if they've never used CAD software before. The process involves uploading and orienting a workpiece in a web interface, and using simple tools to build a support structure around it that will keep it firmly in place. Most actions are a simple click away in the interface, much like writing a document or an email. It can output STL files, so it easily integrates with a 3D printing workflow.
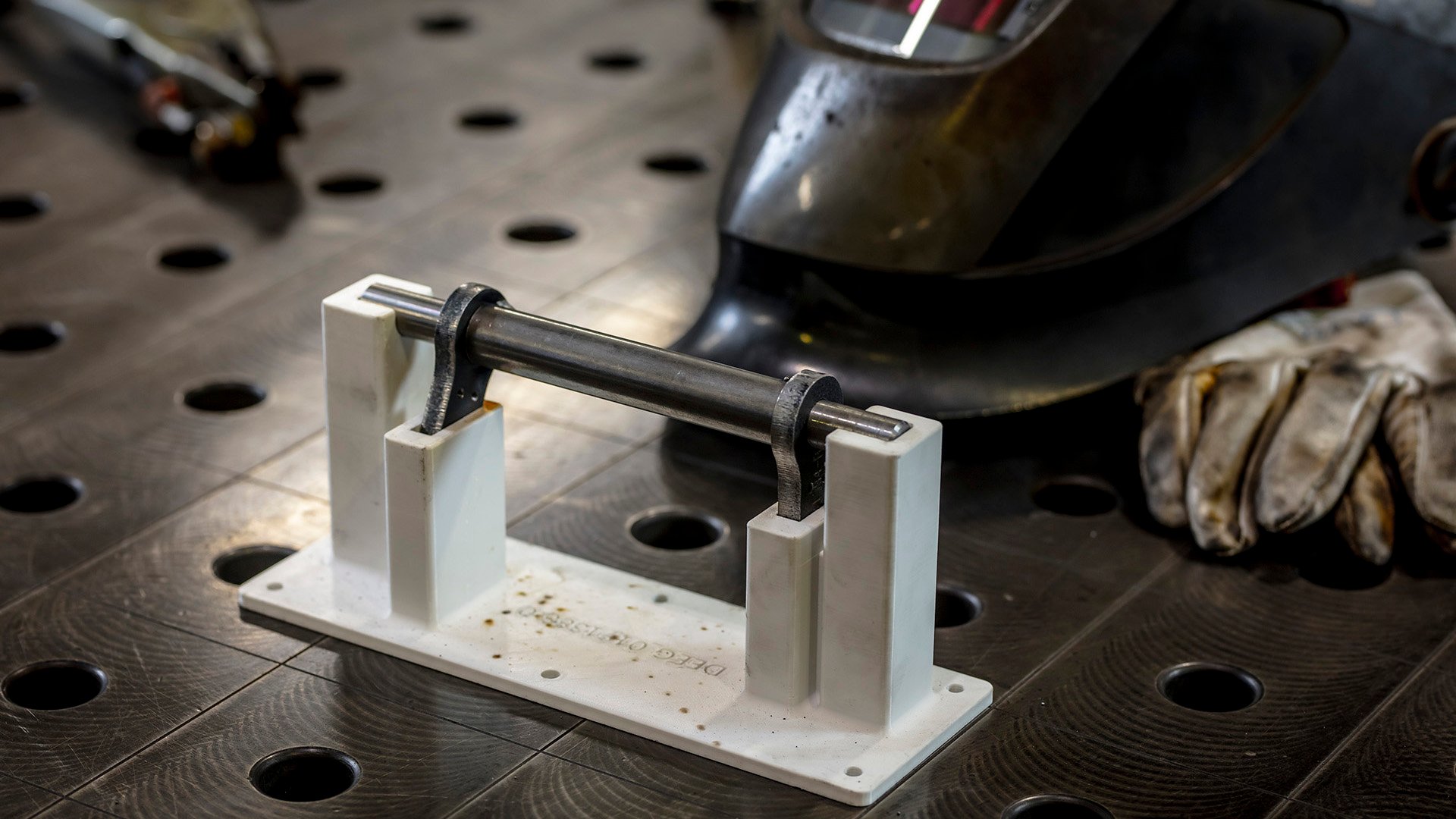
This is a 3D printed welding fixture to fabricate a component used in an industrial vehicle. It keeps two cams at offset angles from each other, which is essential for this application. Fixturing in this way makes the task simple and repeatable, enhancing the quality of the process and avoiding scrap costs and rework.
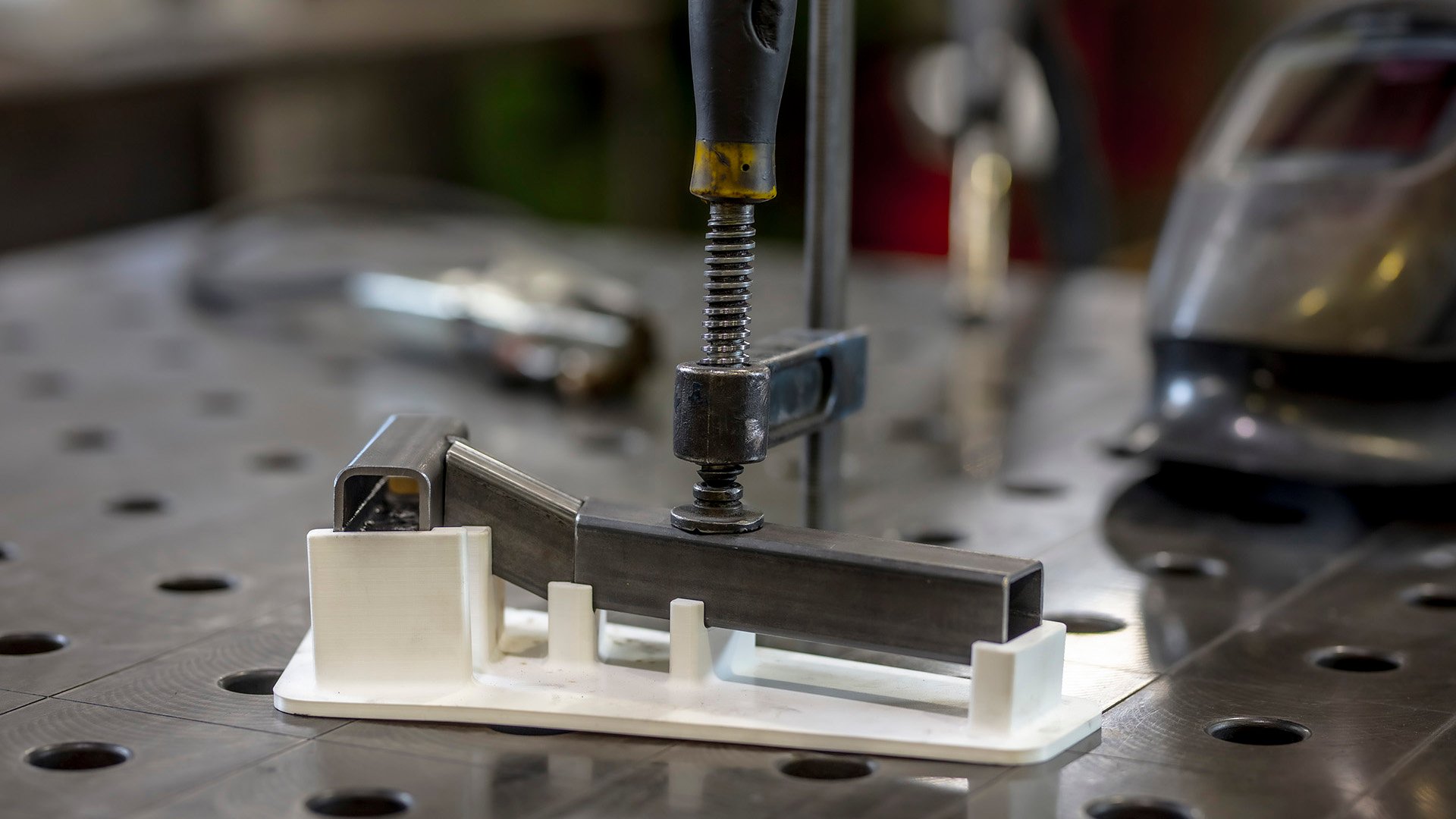
In this example, each component to make this part is kept at a repeatable horizontal angle for welding. The assembly is raised off the surface, which makes it easier to target the edges of each component for a reliable weld.
3D printed fixtures are cheap to produce – much cheaper than any metal. They're durable enough to withstand the heat of welding, even with "basic" 3D printing materials like PLA. They’re also easy to replace at the end of their useful service life. If more fixtures are needed, they can be produced on a low-cost 3D printer within hours. Everything happens locally, so there’s lots of process flexibility for design alterations if they are needed, without expensive consequences most have come to expect with fabrication. Plus, a process that traditionally takes weeks is compressed into a matter of days – or less!
How could design automation help you?
Bonding and welding fixtures play a crucial role in ensuring precise and reliable part quality. You can optimize the design process for these fixtures using our web-based design automation software. Just input some basic settings, draw simple shapes using your mouse, and the software will produce a practical custom design that can save you a good chunk of time and money.
Discover how our design automation software can help you get the design results you want in half the time or less.